A manual task refers to any activity requiring a person to use any part of their muscular or skeletal system within their work environment to get jobs done. This includes:
• Lifting
• Carrying
• Striking
• Pushing
• Pulling
• Throwing
• Holding
All these actions are relevant, and if it means repeating something, maintaining a sustained posture, or exposing yourself to vibrations, then you are carrying out manual handling tasks.
The nature of some jobs means that these activities are frequent every working day, which is why manual handling is so relevant to the workplace. If these actions involve particularly heavy loads, or straining the individual, this is when incidents happen and injuries occur.
Musculoskeletal Disorders (MSD) are the particular problems that come from manual handling. An MSD is an injury affecting the bones or soft tissue structure of the body. Examples include sprains of ligaments, strains of muscles or tendons, and injuries to the spine, joints, bones or nerves.
Costly Problem
Manual handling incidents equate to 33% of all accidents reported to the Health and Safety Authorities every year, affecting one million people a year and costing the economy billions of pounds in the meantime.
Not only are manual handling accidents an inconvenience to the individual left out of work and in pain, but it also causes a massive drain on resources for the employers. This is because they have to cover costs towards the days lost, a decrease in productivity, legal fees, and the cost of training or retraining staff members. The manageability and preventability of manual handling means that it can easily be avoided, saving everyone a lot of pain and money – so everybody wins!
These problems can occur in the first place for these five reasons, all of which are areas that can be dealt with by employers:
• No risk assessment of work activities
• Lack of safe system of work plans
• Mechanical aids were not provided and maintained
• Adequate training was not provided
• No evidence of work supervision
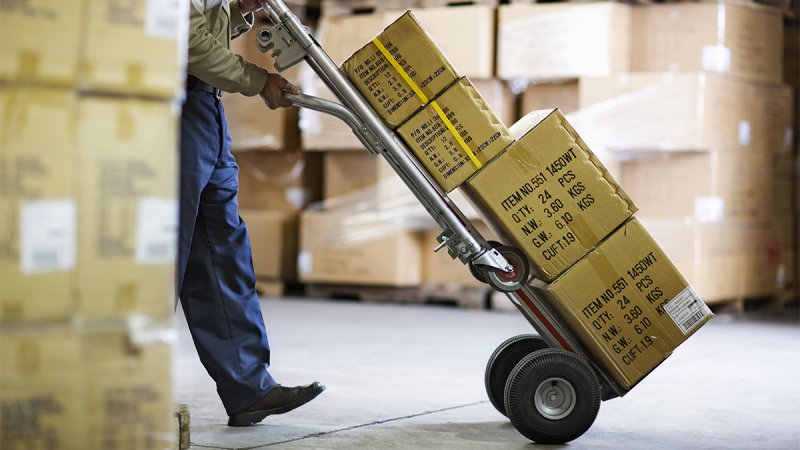
Real Life Story
A 54-year-old library assistant had to move 80,000 books from one area of the library to another over a four-month period. She had to pack the books into boxes that would reach weights of 22kg each! She then had to load them onto trolleys and take them to the new destination.
The librarian hadn’t been trained in manual handling techniques so developed back pain as a result of the persistent heavy lifting. She told her manager about the pain and took three days off to rest. On returning to work she was told to carry on with moving the boxes.
This pain increased to such level that her back eventually seized up altogether, and despite seeking treatment to help her to manage the discomfort, she continued to suffer from chronic back pain which prevented her from working. Her employer didn’t offer her alternative light duties so she was dismissed on grounds of medical incapability.
“I never had any problems with my back before lifting those boxes but now I have to adapt my life around managing the pain.”
Three Steps to Reducing Manual Handling Injuries
1. Identify the manual task hazards
2. Assess the risk of those manual task hazards identified causing injury
3. Eliminate the risk, or if not practicable reduce the risk to the lowest practicable level