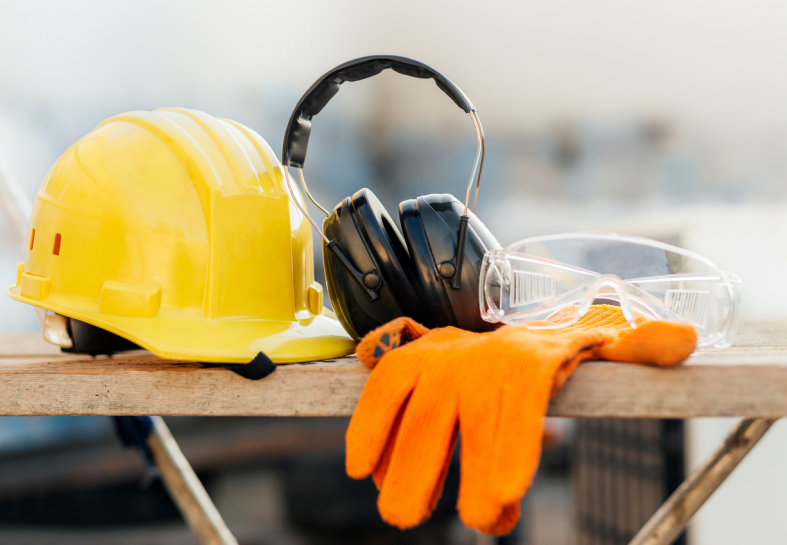
In the last year in the UK, there were over 78,000 reportable injuries at work in the last year. At least 2 million sick days are taken because of back pain – two thirds of which could have been avoided through the use of safe manual handling techniques. Most manual handling injuries actually do not occur as a result of intense or strenuous activities or unexpected events such as a fall, but rather are the result of cumulative strain, i.e. gradual wear and tear caused by day to day tasks.
What is manual handling in the workplace?
Manual handling in the workplace refers to any activity that involves the lifting, carrying, pushing, pulling, or moving of objects or people by hand. It is a common task in many industries and workplaces, ranging from offices to construction sites, warehouses, healthcare facilities, and more.
Manual handling tasks can include activities such as lifting boxes, stacking shelves, moving equipment, transferring patients, and handling tools or machinery. While manual handling is a necessary part of many jobs, it can pose various risks to the health and safety of workers if not performed correctly.
Who is responsible for safe manual handling at work?
In the United Kingdom, the responsibility for safe manual handling at work primarily rests with employers. They have a legal obligation to ensure the health and safety of their employees under the Health and Safety at Work Act 1974 and associated regulations.
The importance of manual handling at work
Effective manual handling practices are of paramount importance in the workplace. By prioritising safe manual handling techniques, employers can significantly reduce the risk of musculoskeletal injuries and promote the overall well-being of their staff. Proper manual handling not only safeguards employees from immediate harm but also helps prevent long-term health problems, such as back injuries and repetitive strain injuries. By providing appropriate training, implementing control measures, and fostering a culture of safety, employers can create a work environment that values the physical health and safety of their employees. Prioritising manual handling safety contributes to increased productivity, reduced absenteeism, and improved job satisfaction, ultimately leading to a more efficient and healthier workplace.
What are the 4 key factors of manual handling?
The four key factors with respect to manual handling are commonly referred to as “TILE.” Each letter in TILE represents an important aspect of manual handling.
- Task: This refers to the nature of the manual handling task being performed, such as lifting, carrying, pushing, or pulling objects. It involves considering the weight, size, and shape of the objects being handled.
- Individual: This factor focuses on the capabilities of the individual involved in manual handling. Considerations include their physical fitness, experience, training, and any pre-existing medical conditions or limitations.
- Load: The load factor involves assessing the characteristics of the object being handled. This includes its weight, stability, shape, size, and any potential hazards associated with it. It also encompasses factors such as the need for team lifting or the use of mechanical aids.
- Environment: The environment factor considers the surrounding conditions in which manual handling takes place. This includes factors such as the layout of the workspace, the presence of obstacles or uneven surfaces, lighting, temperature, and any other potential hazards or risks present in the environment.
Manual handling at work: a guide
VinciWorks and DeltaNet have produced a valuable, in-depth guide to manual handling. The guide provides a background to the topic and explains what the risk factors are with regard to cumulative strain caused by manual handling. The guide sets out the legal requirements on employers and goes through different types of manual handling and the risks involved in each type. Readers are taught how to identify red flags, how to conduct a risk-assessment, and how to reduce the risk of injuries.
Any organisation whose workers engage in manual handling will benefit from this guide that sets out your legal obligations as an employer, explains the risks and how to make sure workers are able to perform their jobs safely and effectively and prevent lost productivity, increased absenteeism and reduced quality of life for affected workers.
Manual handling training
Training is a key factor in reducing injury and accidents from manual handling; click to learn more about our manual handling training and manual handling challenge courses.
Health and safety training
DeltaNet provide market-leading Compliance, Health and Safety, and Performance online training solutions that fit the needs of your business. Click here to learn more.
FAQs on manual handling training
What is manual handling training?
Manual handling training refers to the process of educating individuals on safe techniques and practices for handling objects manually.
What is the purpose of manual handling training?
The purpose of manual handling training is to provide individuals with the necessary knowledge and skills to minimise the risk of injuries and promote safe working practices when lifting, carrying, pushing, or pulling objects.
Do staff need to do manual handling training?
All staff members that are involved in manual handling activities should undergo manual handling training. It’s important for organisations to provide this training to ensure the safety and wellbeing of their employees.
How long does manual handling training take?
The duration of manual handling training can vary depending on several factors, including the specific content being covered, the training provider, and the needs of the participants. Generally, manual handling training courses range from a few hours to a full day. The specific duration of manual handling training should be determined based on the needs of the participants and the scope of the training program being implemented.
Is manual handling training a legal requirement?
Under UK health and safety regulations (Manual Handling Operations Regulations 1992), employers have a legal duty to assess and manage the risks associated with manual handling activities.